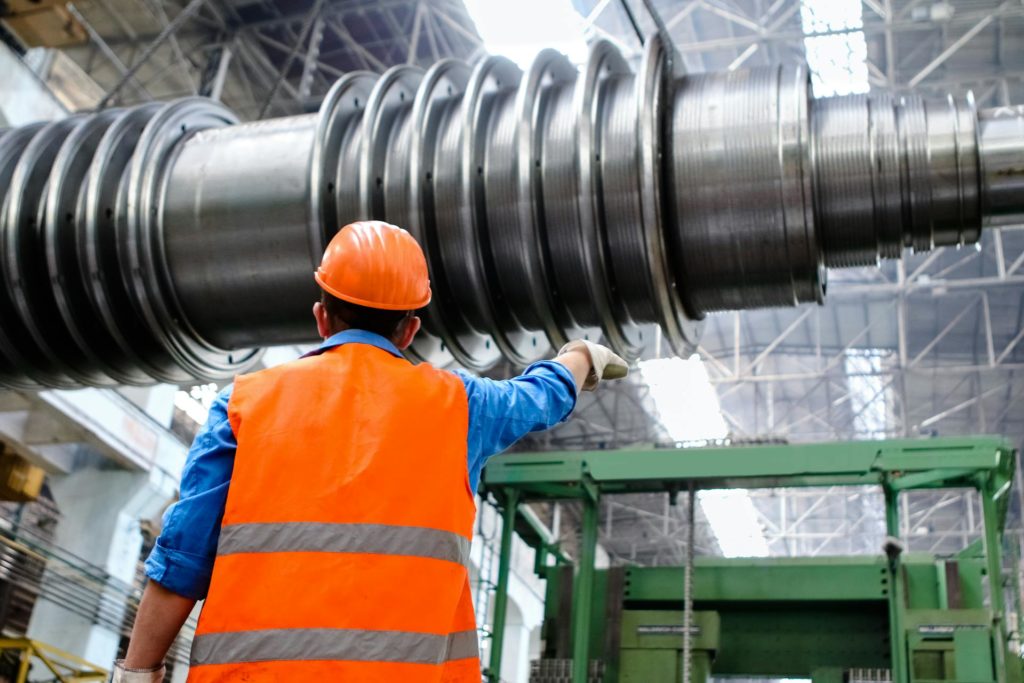
In today’s evolving world، effective manufacturing management software isn’t merely a luxury – it’s a must-have. The complexity of manufacturing operations is growing by the day،. Picking the software can mean distinguishing between smooth operations and disorder in the workplace. To assist you in making an informed choice, here are some essential elements to consider while choosing manufacturing management software.
Integration Capabilities
One key aspect of custom manufacturing software is its ability to smoothly integrate with systems, like ERP and CRM tools, for supply chain management. Your software needs to have integration features that break down data barriers and promote teamwork. This way, every department can access up-to-date information, facilitating better decision-making and operational productivity.
Real-Time Data Analysis
In industries like manufacturing, where timing’s crucial, having the capacity to access and evaluate data instantly is essential for making decisions, efficiently and effectively managing resources, and optimally planning for the future! Seek software that offers data analysis and visualization capabilities to drive problem-solving responses and enhance operational efficiency. This leads to increased productivity through continuous optimization efforts based on real-time insights.
Inventory Management
A reliable manufacturing management system should have a range of inventory control capabilities, such as monitoring materials in use during production and tracking the progress of unfinished items until they become finished products ready for sale or distribution. This process is critical for maintaining the amount of inventory on hand to minimize expenses related to storage and warehouse management while avoiding disruptions in production caused by material shortages. Implementing automated inventory tracking also offers data on how inventory is moving through the production process and can support efficient, just-in-time manufacturing practices.
Production Planning and Scheduling
Efficient planning and scheduling play a significant role in the success of manufacturing operations. Find a software solution that includes planning and scheduling (APS). This tool will help you optimize production workflows and ensure load capacities while efficiently utilizing labor resources. Automation in scheduling can reduce downtime. Enhance the efficiency of your manufacturing operations.
Quality Control Features
Ensuring top-notch quality is a must in manufacturing processes. Your software ought to have quality management capabilities, like overseeing inspections, handling compliance documentation, and incorporating preventive actions (CAPAs). These functionalities will help uphold quality standards, minimize waste, and guarantee that your goods satisfy customer demands. Quality control measurements can also drive enhancement efforts.
User-Friendly Interface
When choosing a software solution packed with features, make sure it’s user-friendly, too! Opt for software with an intuitive interface to make it easier for users to learn and use without hassle or training. This way, employees can easily navigate the system to input data and create reports smoothly, boosting efficiency and minimizing mistakes in the long run.
Scalability Capability
As your manufacturing company expands in size and scope, it is vital that your software systems expand alongside it. The ability to scale smoothly is crucial when selecting management software for manufacturing operations. It’s important to verify that the chosen solution is capable of managing production quantities, a range of inventory items, and increased user accessibility without experiencing any performance issues. Scalable software also offers the flexibility to incorporate functionalities and integrations as your operational requirements continue to develop and change over time.
Mobile Access
In this era of technological advancements, having the ability to access your manufacturing management software through devices can truly make a difference in how things operate. This convenient feature empowers managers and staff members to retrieve data and complete tasks whether they are working remotely or right at the production site. By enabling access, work processes can run seamlessly regardless of the locations of team members, ultimately facilitating quicker decision-making and improving communication across different departments.
Security and Compliance
In light of the growing risks associated with data security breaches, it’s crucial to have protection measures in place for your software. These measures should involve implementing access controls based on roles, encrypting data, and using communication protocols. Moreover, the software should assist you in adhering to industry regulations and standards, whether they relate to safety concerns or safeguarding data. This helps safeguard information and ensures that the company operates in accordance with its obligations.
Support and Training
Consider the support and training provided by the software provider well. Customer support plays a key role in resolving any issues that may arise and minimizing downtime. Comprehensive training programs are essential to help your team use the software’s capabilities.
Conclusion
To sum up the decision-making process, selecting manufacturing management software involves evaluating these essential characteristics. Opting for a solution that aligns with your specific needs can elevate efficiency and product quality while fostering expansion in your manufacturing enterprise.