The automobile industry has been one of the significant contributors to revenue generation in the powder metallurgy (PM) field. Modern cars must be lightweight to perform well, have better fuel efficiency, and provide road safety. The sturdiness of their overall composition depends on the various parts that ultimately make them. Auto parts made through older metalworking systems either failed to have consistency in shape or size or lacked the desired material properties due to intensive manufacturing. Delayed supply became another challenge. At the same time, most of these processes don’t conform to environmentally friendly practices. Fortunately, powder metallurgy changed these scenarios. This metal-forming process benefits fuel-powered and automatic transmission vehicles today.
Powder Metallurgy Benefits for Automotive Industry
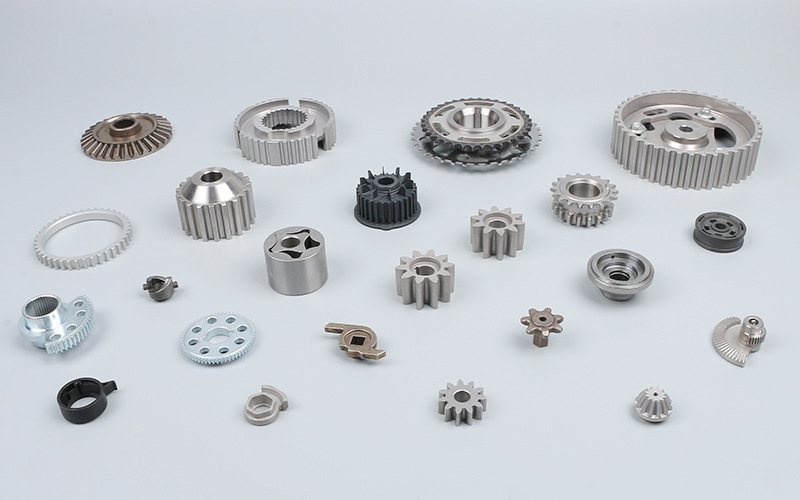
PM has become integral to transforming the automobile manufacturing industry by offering stronger and lightweight components. The powder metallurgy products are made from compressed and sintered metal powder. These techniques help create parts with complex geometries while retaining the best base material properties. The impact of this system can especially be witnessed in the area of transmission gears, which must be highly wear-resistant, strong, and efficient. Check spur, bevel, helical, and planetary gear for an idea. Some are required in fuel-powered vehicles, while others are more suitable for electric cars. PM engineers mix various alloys to improve these gears’ wear resistance and strength. High-quality gears increase cars’ operational efficiency and long-lastingness.
For electric vehicles, another advantage is that PM technology helps produce self-lubricating parts that reduce friction in the central systems and improve their energy efficiency. If you are committed to green goals, you can embrace these components to promote your sustainability efforts. The entire manufacturing process focuses on the optimal use of the original material, eliminating secondary machining steps that consume more energy. Due to these factors, auto components become much more affordable. One key process that extensively contributes to powder metallurgy’s green impact is sintering. At this stage, pressed metal powder is exposed to high temperatures (lower than the material’s melting point) to allow the particles to combine and form a desired porous or solid object. Through sintering, many types of components are created for cars.
Eco-Friendly Tech Advances in Sustainable Automotive Technology
Sintered Metal Parts for Automakers
You can look for self-lubricating bearings, crankshaft timing gears, valve seat inserts, clutch hubs, etc. Or do you want something specifically to improve your car engine’s performance and cooling? In that case, a sintered water pump flange can help. The water pump flange connects the pump and the cylinder head to circulate coolant and stop leakage risks. Otherwise, the engine can fail due to overheating. Sintered products are often corrosion-resistant, too. As a consequence, these don’t wear out soon.
Precision and cost-effectiveness are the added advantages of most PM products. The automotive industry is exceptionally agile and must keep pace with the market. With these efficient solutions, you can significantly reduce your material sourcing stress. You can get the repeat designs in bulk without a long waiting period. As hinted, these objects are also eco-friendly because of the specific manufacturing practices. Hence, it can be worth considering them. You can also try the customization option if you need something in a different dimension or size.